Manufacturing
REVOLUTIONIZING THE ORDINARY
OUR APPROACH TO PRODUCTION
Our products are shaped not just by technology but also by our challenger spirit and unwavering dedication to craftsmanship. By pushing boundaries and refining innovation, we aim to infuse every lens and camera with a distinct soul. Our high-performing lenses and cameras are proof of that.
Not only in Japan, but also people living in third-world countries like Pakistan have queries about the digital camera price in Pakistan.This progressive mindset is reflected in our engineers' exploration of new technologies and our skilled workers' unwavering attention to detail in perfecting each product. Collaboration across departments brings diverse skills and ideas together, turning visions into tangible realities.
Creating a Sigma product is far from a rigid or standardized process—it is dynamic and driven by continuous creativity and open dialogue. And when the technology to bring an idea to life doesn't exist, we create it.
BEYOND DISCIPLINES
Sigma centers its efforts on three main areas: development, manufacturing, and services. These together form the core of our offering. Our products are designed and developed at our headquarters and brought to life at our Aizu factory. Our services including our distinctive lens repair service reflect the same careful attention to detail that defines our development and production processes.
At Sigma, product development is built on the collaboration of knowledge and technology. We continuously gather valuable input by sharing ideas, innovations, and insights across departments. These insights inspire new ideas and solutions, which come together to form our products.
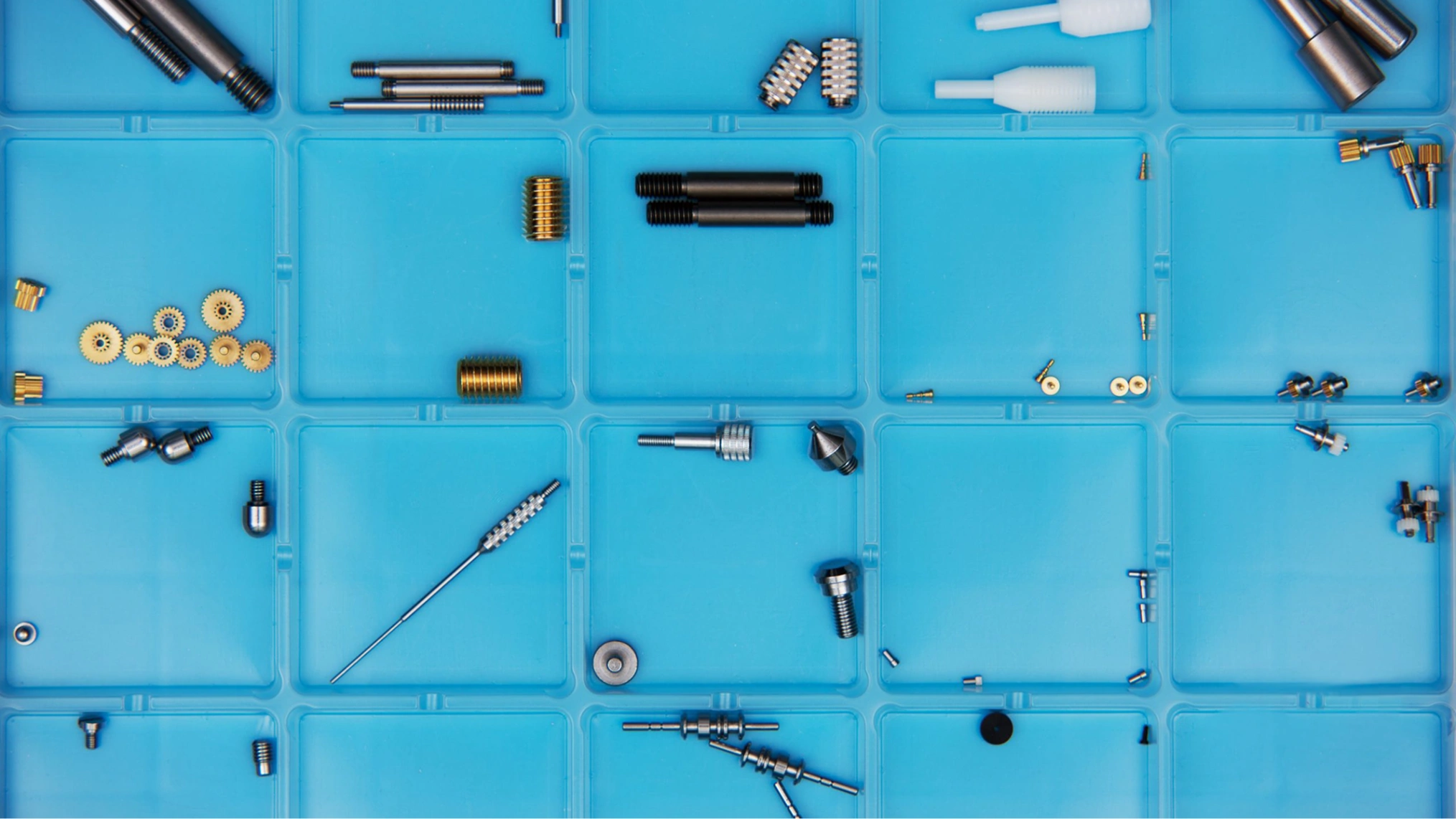
SMALL OFFICE, BIG FACTORY
At Sigma, we uphold the principle of "camera shop near me, big factory," which embodies the harmony of creativity and technology at the heart of our production system.
Our office is where ideas are born, and our factory is where they are transformed into high-quality products. The process often moves quickly, starting with concepts for lenses designed to enhance photographers' creativity or groundbreaking innovations we aim to achieve. Once a prototype is developed, we bring it to life at our Aizu facility using advanced manufacturing technologies.
This approach relies on a seamless integration of human ingenuity and technological precision, a balance central to our philosophy. Over the years, this interaction between people and machines has been continually refined, supported by the concentration of our production, research, development, and assembly processes in one country for decades.
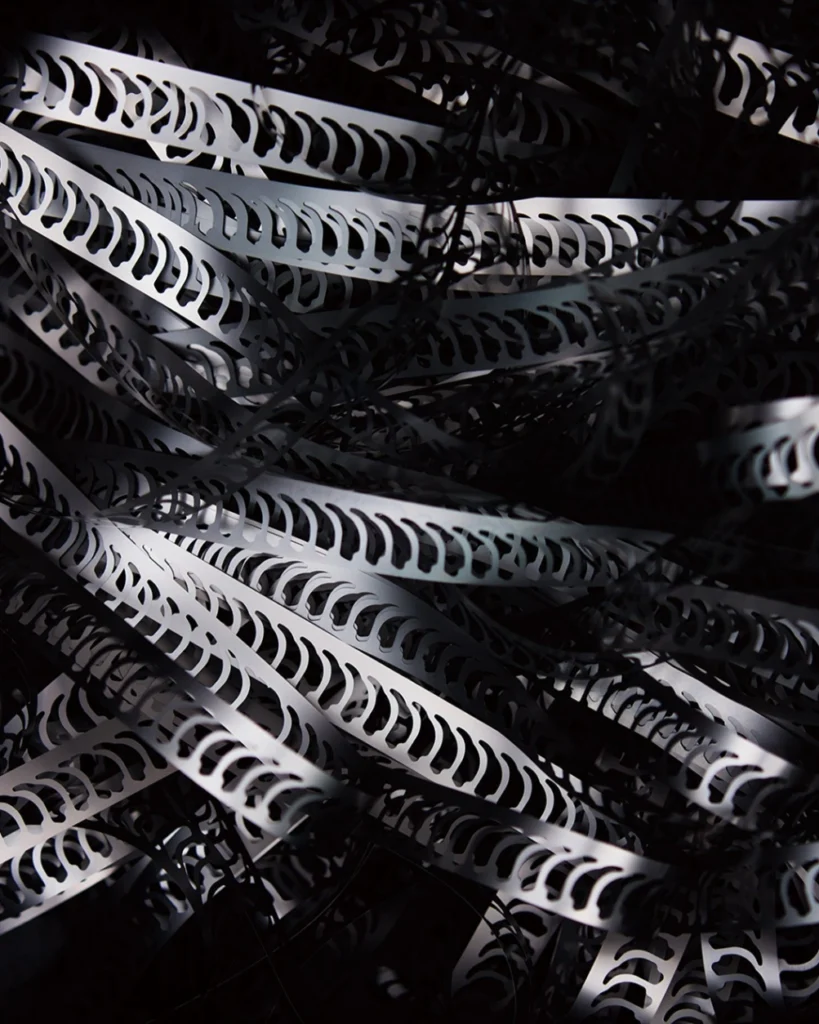
STAYING VERTICAL AN INTEGRATED SUPPLY CHAIN
Since our founding in 1961, Sigma’s entire production system has been based in Japan. Unlike most production chains in today’s globalized world, we create and customize all components at our factory in Aizu or in partnership with local businesses in the Tohoku region. Our Aizu factory has been in operation since 1973.
This single-region production system offers several advantages. Direct, face-to-face communication allows for faster and more careful product development. It also means the same skilled people are involved in manufacturing, allowing them to build experience and knowledge that lead to new ideas and improvements.
These qualities demand a comprehensive and instinctive understanding, which we view as an invaluable asset. This is why our fully integrated, Japan-based production system is so important to us.
INNOVATION PERFECTED: OUR PRODUCTION AT A GLANCE
We are passionate about delivering the best possible quality in optics. As devoted photography enthusiasts, We share a strong bond with passionate photographers and truly respect their expressive ambitions. Explore the examples below that highlight our uncompromising commitment to quality.
This standard was established by Sigma's founder, Michihiro Yamaki, for the production process. He frequently said these words during his visits to the Aizu factory, ensuring all operations ran smoothly, like water through a river.
Currently, there is no single universal mount that fits all interchangeable camera systems on the market. Therefore, following our manufacturing plan's model numbers, we produce about 200 different lens variations at our Aizu factory.
Sigma's spherical lenses are made with an incredibly precise surface roughness of only 2 micrometers. Surface roughness measures how much the surface differs from a perfectly smooth one. In perspective, if a lens were enlarged to 300 kilometers in diameter—the distance from Tokyo to Aizu—the most significant bump would be less than 2 centimeters.
The largest single lens we manufacture is the front element of the APO 200-500mm F2.8 EX DG, which has a diameter of 198mm. Applying its lens coating requires a careful eight-hour process.
On the other hand, the smallest lens in our range is the 7th element of the 8-16mm F4.5-5.6 DC HSM zoom lens, measuring only 10mm.
*As of 2017
Since the launch of Sigma Global Vision in 2012, we have been engraving a three-digit code on each lens. This code indicates the model's release year. We hope this detail allows customers to feel closer to their product by placing it within Sigma's production history—similar to how vintage wine is valued.
The three-digit code is engraved using an excellent end mill. This delicate process is done with great care and takes about three minutes for each lens.
Our brass bayonets are coated with thick chrome plating, providing a durable, scratch-resistant finish. We began using trivalent chromium in our production as soon as it became available for industrial use. This type of chromium meets our requirements perfectly, with a plating thickness of less than 0.5 micrometers. By choosing trivalent chromium over the highly toxic hexavalent chromium, we prioritize the health of our workers and reduce our factory's environmental impact.
When designing and producing molds, the finishing process is carefully examined in great detail. For precise adjustments, we often work with measurements in micrometers (0.000001m).
Since Sigma Global Vision launched in 2012, every lens we ship has been measured and quality-checked using Sigma's MTF measuring device. Accurate measurement data for each lens is stored at our Aizu facility.
We focus heavily on the processing technologies used to create molds for parts that require extreme precision, like lens cells. Our machines at the Aizu factory maintain manufacturing deviations within 0.002mm, which is more accurate than even the most advanced ultrahigh precision 3D measuring devices. We are dedicated to achieving the highest level of precision at every stage of the process, beyond what current measuring tools can detect.
Our quality control team ensures that every product performs perfectly and looks flawless. They also check essential features that are hard to measure, like how smoothly the zoom and focus rings turn. Our evaluation standards are incredibly strict—if a ring "doesn't feel quite right," the product can be taken apart and rebuilt.